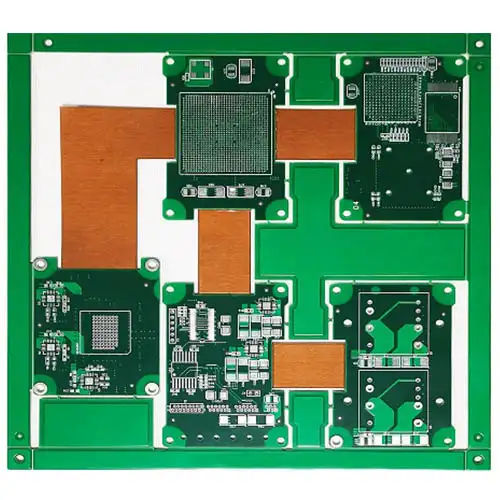
8-layer 1-stage HDI rigid-flex board
Name: 8-layer 1-stage HDI rigid-flex board
Plate: NPG-170
Plate thickness: 1.2 mm
Layers: 8 layers
Minimum line width/line spacing: 3/3 mil
Finished copper thickness: inner layer 0.5OZ, outer layer 1OZ
Acceptance Criteria: IPC6012 CLASS Level 2
Surface Technology: Immersion Gold
Dielectric constant: 4.2
Loss factor: 0.010
Use: medical equipment
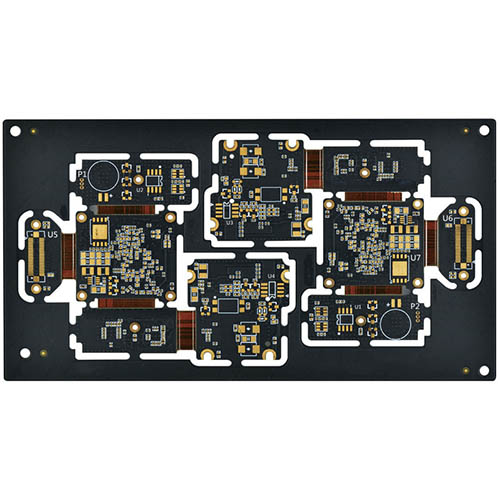
10-layer 2-stage HDI rigid-flex board
Name: 10-layer 2-stage HDI rigid-flex board
Plate: Taiguang EM-888S
Plate thickness: 1.0 mm
Layers: 10 layers
Minimum line width/line spacing: 4/4mil
Finished copper thickness: inner layer 0.5OZ, outer layer 1OZ
Acceptance Criteria: IPC6012 CLASS Level 3
Surface Technology: Immersion Gold
Dielectric constant: 3.8
Loss factor: 0.0055
Use: security monitoring equipment
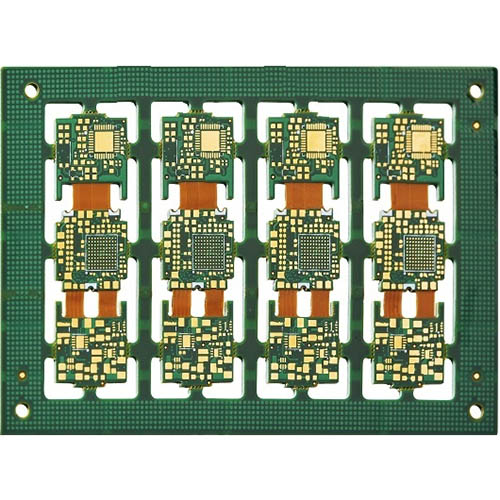
8-layer 2-stage HDI rigid-flex board
Name: 8-layer 2-stage HDI rigid-flex board
Layers: 8L
Structure: 3F+5R (8-layer 2-level HDI)
Sheet Type: PI, PET, PEN
Minimum hole: 0.1mm
PI thickness: 0.5mil-2mil
Cu Thickness: 1/3oz-2oz
Minimum line width/line spacing: 0.1/0.1mm;
NPTH Finished Aperture Tolerance: ±1mil(±0.025mm)
PTH Finished Aperture Tolerance: ±2mil(±0.050mm)
Finished plate thickness tolerance: ±0.01mm
Minimum line width/line gap: 0.05/0.05mm
Application field: High-end precision industrial sensor control board
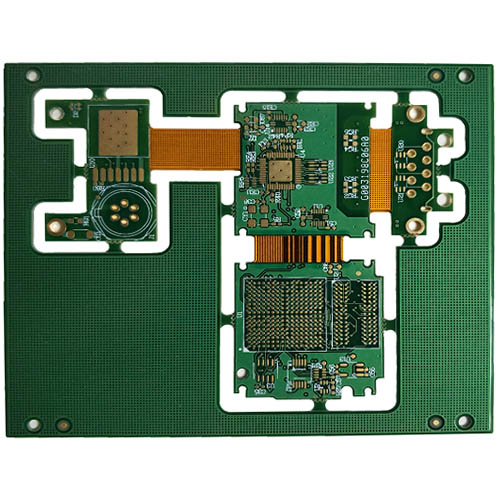
10-layer 2-stage HDI rigid-flex board
Name: 10-layer 2-stage HDI rigid-flex board
Plate: Taiguang EM-888S
Plate thickness: 1.0 mm
Layers: 10 layers
Minimum line width/line spacing: 4/4mil
Finished copper thickness: inner layer 0.5OZ, outer layer 1OZ
Acceptance Criteria: IPC6012 CLASS Level 3
Surface Technology: Immersion Gold
Dielectric constant: 3.8
Loss factor: 0.0055
Use: security monitoring equipment
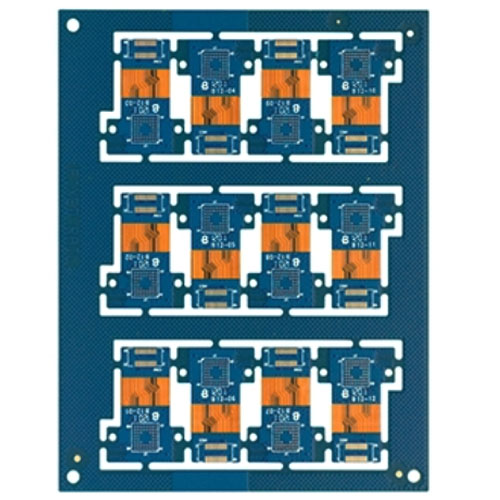
Name: 8-layer rigid-flex PCB board
Layers: 8L
Plate thickness: 1.45mm
Minimum aperture: 0.25mm
Minimum line width/line spacing: 5/3.6mil
Inner layer copper thickness: HOZ
Outer copper thickness: 1OZ
Surface treatment: chemical gold ENIG
Minimum distance from hole to line: 0.25mm
Application field: consumer electronics
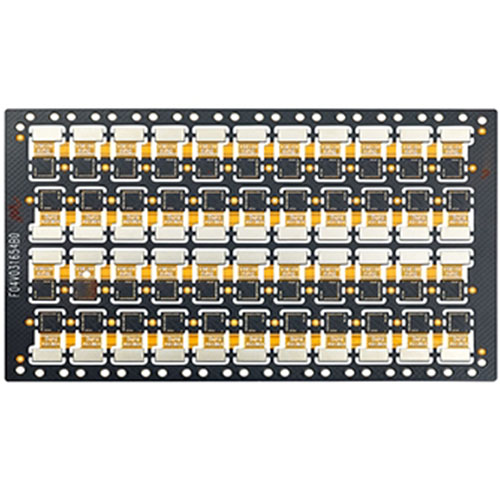
Name: 8L rigid-flex board
Layers: 8L
Plate thickness: 1.45mm
Minimum aperture: 0.25mm
Minimum line width/line spacing: 5/3.6mil
Inner layer copper thickness: HOZ
Outer copper thickness: 1OZ
Surface treatment: chemical gold ENIG
Minimum distance from hole to line: 0.25mm
Application field: consumer electronics
- Rigid Flex PCB Capability
- PCB manufacturing equipment
Introducing the Rigid Flex PCB, a cutting-edge solution for all your circuit board needs. Designed with advanced technology, this PCB combines the flexibility of a flexible circuit with the rigidity of a traditional printed circuit board (PCB). The Rigid Flex PCB is perfect for applications that require both compactness and durability. With its unique design, it enables the creation of complex three-dimensional shapes, making it ideal for space-constrained electronic devices.
The Rigid Flex PCB offers unparalleled reliability and stability, thanks to its rigid sections that provide support and protection to sensitive components. The flexible sections allow for easy bending and folding, facilitating efficient routing and reducing the need for connectors and cables. This not only simplifies assembly but also improves signal integrity and reduces electromagnetic interference.
With the Rigid Flex PCB, you can achieve higher component density and reduce the overall size and weight of your electronic devices. Its robust construction ensures resistance to vibrations, shocks, and extreme temperatures, making it suitable for various industries such as aerospace, automotive, medical, and consumer electronics.
The capabilities of rigid-flex PCBs vary depending on the specific manufacturer and their equipment, expertise, and production processes. However, here are some common capabilities associated with rigid-flex PCB manufacturing:
- Layer count: Rigid-flex PCBs can be manufactured with multiple layers to accommodate complex circuit designs. The layer count can range from a few layers to several layers, depending on the requirements of the application.
- Material selection: Rigid-flex PCBs typically use a combination of rigid substrates (such as FR-4) and flexible materials (such as polyimide or PET) to achieve the desired mechanical and electrical properties. Manufacturers can provide guidance on material selection based on the specific application and performance requirements.
- Circuit design complexity: Rigid-flex PCBs can support complex circuit designs, including high-density interconnections, fine pitch components, and impedance-controlled traces. Advanced manufacturing techniques like laser drilling and microvia technology enable precise routing and interconnection between rigid and flexible sections.
- Size and shape flexibility: Rigid-flex PCBs offer flexibility in terms of size and shape. They can be customized to fit within the available space and conform to the mechanical constraints of the application. This flexibility allows for efficient use of space and integration into three-dimensional designs.
- Surface finishes and solder mask options: Rigid-flex PCBs can be manufactured with various surface finishes, such as HASL (Hot Air Solder Leveling), ENIG (Electroless Nickel Immersion Gold), or immersion silver, based on specific requirements. Solder mask options include different colors and materials to provide protection and insulation.
- Assembly and testing: Rigid-flex PCB manufacturers often offer assembly and testing services, including component placement, soldering, inspection, and functional testing. This ensures a streamlined production process and quality control.
Advantages of Rigid-Flex PCB :
- Space Optimization: The Rigid Flex allows for efficient use of space, enabling designers to create smaller and more compact electronic devices.
- Improved Reliability: The combination of rigid and flexible sections enhances the durability and stability of the PCB, reducing the risk of component failure.
- Simplified Assembly: With fewer connectors and cables required, the assembly process becomes more streamlined and less prone to errors.
- Enhanced Signal Integrity: The Rigid Flex minimizes signal loss and electromagnetic interference, ensuring reliable and high-quality performance.
- Cost Savings: Despite its advanced technology, the Rigid Flex PCB can help reduce overall manufacturing and assembly costs by eliminating the need for additional components and simplifying the production process.
PCB Drilling machine
PCB pattern plating line
PCB solder mask expose machine
PCB pattern expose machine
Strip film etching line
Solder mask screen silk print machine
Solder mask scrubbing line
PCB Flying Probe Test (FPT)
Fully automatic exposure machine