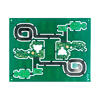
Rigid-Flex Low Volume PCB Assembly – Perfect for Aerospace
Name: Rigid-Flex Low Volume PCB Assembly – Perfect for Aerospace
Origin: China
Certified: UL, CE, RoHS
Base Material: Copper or aluminum
Copper Thickness: 2oz
Surface Finishing: Gold Finger, Immersion Silver, Immersion Tin
Solder mask color: Yellow. Optional
Application: Consumer Electronics
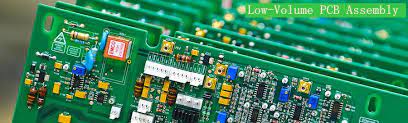
Flex Low Volume PCB Assembly for Digital Cameras and Cell Phones
Name: Flex Low Volume PCB Assembly for Digital Cameras and Cell Phones
Origin: China
Certified: UL, CE, RoHS
Base Material: Copper or aluminum
Surface Finishing: Gold Finger, Immersion Silver, Immersion Tin
Copper Thickness: 2oz
Solder mask color: Yellow. Optional
Board Thickness: customized
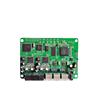
High Frequency Low Volume PCB Assembly
Name: High Frequency Low Volume PCB Assembly
Origin: China
Certified: UL, CE, RoHS
Surface Finishing: OSP, HASL, Immersion gold, Immersion Tin etc.
Copper Thickness: 1OZ,2OZ,3OZ 4OZ 5OZ Customization
Board thickness: 0.3-3.5mm
Solder mask: Green ,Black, Blue, Red, white etc.
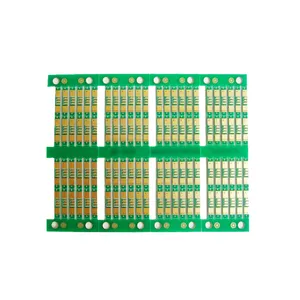
Heavy Copper Low PCB Assembly for Electronic
Name: Heavy Copper Low PCB Assembly for Electronic
Origin: China
Certified: UL, CE, RoHS
Copper Thickness: 1 oz
Solder Mask Color: Double-sided green LPI, Also support red, white, yellow, blue, black
Board thickness: customized
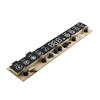
HDI Low Volume PCB Assembly especially for Equipment
Name: HDI Low Volume PCB Assembly especially for Equipment
Origin: China
Certified: UL, CE, RoHS
Copper Thickness: 4 oz
Application field: LED LIPS
Copper Thickness: 4 oz
Board thickness: Mass production: 394mil(10mm) Samples: 17.5mm
Layer: 1-64 L
Surface finish: HASL, OSP, Immersion Gold/Silver/Tin, ENIG, Gold Finger
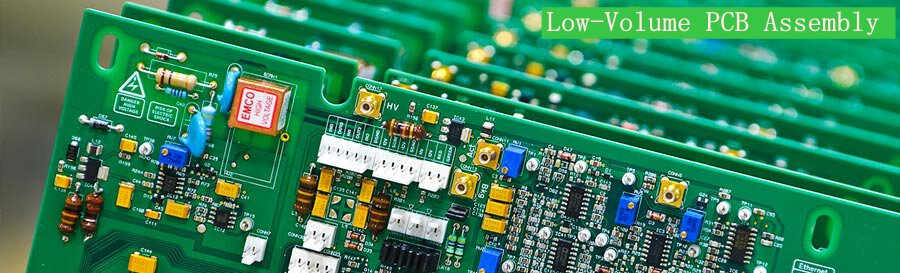
LED Low Volume PCB Assembly for Consumer Application
Name: LED Low Volume PCB Assembly for Consumer Application
Origin: China
Certified: UL, CE, RoHS
Surface Finishing: OSP, HASL, Immersion gold, Immersion Tin etc.
Solder mask: Green, Black, Blue, Red, white etc.
Board thickness: 0.3-3.5mm
Copper Thickness: 1OZ,2OZ,3OZ 4OZ 5OZ Customization
- PCB Assembly Capability
- PCB Assembly Equipment
Low Volume PCB Assembly is a specialized electronic manufacturing service that caters to the production of printed circuit boards (PCBs) in small quantities. It is designed to accommodate low-volume production runs, prototypes, or custom-made PCBs that do not require large-scale manufacturing processes.
Low Volume PCB Assembly offers cost-effective solutions for projects with lower production quantities, providing flexibility, customization, and quick turnaround times. It is ideal for applications such as research and development, proof-of-concept prototypes, specialized equipment, and niche markets.
Key Features and Advantages of Low-Volume PCB Assembly:
- Flexibility and Customization: Low Volume Assembly offers flexibility in accommodating customized designs, specific requirements, and design iterations. It allows for the incorporation of unique components, specialized features, and custom layouts to meet the specific needs of the project.
- Cost-Effectiveness: Low Volume Assembly is cost-effective for small production quantities, as it eliminates the high upfront costs associated with large-scale production processes. It allows for cost optimization without sacrificing quality. This makes it suitable for projects with budget constraints or limited market demand.
- Quick Turnaround Time: Low Volume Assembly typically provides faster turnaround times compared to high-volume production. With streamlined processes and reduced manufacturing queues, the assembly can be completed more rapidly. This enables prompt delivery of prototypes or low-volume PCB orders.
- Design Validation and Prototyping: Low Volume Assembly is an excellent choice for design validation and prototyping purposes. It allows engineers and designers to test and refine their designs before moving to full-scale production. It also provides an opportunity to identify and address any design issues, functionality concerns, or performance improvements at an early stage.
- Quality Control and Testing: Despite the lower production quantities, Low Volume PCB Assembly still adheres to rigorous quality control and testing processes. This also ensures that each assembled PCB meets the required specifications and functionality. Testing may include visual inspection, automated optical inspection (AOI), functional testing, and other relevant quality assurance measures.
SMT capacity: 19 million points/day | ||
Testing Equipment | X-RAY Nondestructive Tester, First Piece Tester, AOI Automatic Optical Tester, ICT Tester, BGA Rework Station | |
Placement speed | Chip placement speed (at best conditions) 0.036 S/piece | |
Mounted Component Specifications | Pasteable smallest package | |
Minimum device accuracy | ||
IC type chip accuracy | ||
Mounted PCB Specifications | Substrate size | |
Substrate thickness | ||
throw rate | 1. Resistance-capacitance ratio 0.3% | |
2. IC type without throwing material | ||
Board Type | POP/common board/FPC/rigid-flex board/metal substrate | |
DIP daily production capacity | ||
DIP plug-in production line | 50000 points/day | |
DIP post welding production line | 20000 points/day | |
DIP test production line | 50000pcs PCBA/day | |
Assembly processing capability | ||
The company has more than 10 advanced assembly production lines, dust-free and anti-static air-conditioning workshop, TP dust-free workshop, equipped with aging room, test room, functional test isolation room, advanced and perfect equipment, can carry out various product assembly, packaging, testing, Aging, etc. production. Monthly production capacity can reach 150,000 to 300,000 sets/month | ||
PCBA processing capability | ||
project | Mass processing capability | Small batch processing capability |
Number of layers (max) | 2-18 | 20-30 |
Plate type | FR-4, Ceramic Sheet, Aluminum Base Sheet PTFE, Halogen Free Sheet, High Tg Sheet | PTFE, PPO, PPE |
Rogers,etc Teflon | E-65, ect | |
Sheet mixing | 4 layers – 6 layers | 6th floor – 8th floor |
biggest size | 610mm X 1100mm | / |
Dimensional Accuracy | ±0.13mm | ±0.10mm |
Plate thickness range | 0.2mm–6.00mm | 0.2mm–8.00mm |
Thickness tolerance ( t≥0.8mm) | ±8% | ±5% |
Thickness tolerance (t<0.8mm) | ±10% | ±8% |
Media thickness | 0.076mm–6.00mm | 0.076mm–0.100mm |
Minimum line width | 0.10mm | 0.075mm |
Minimum spacing | 0.10mm | 0.075mm |
Outer copper thickness | 8.75um–175um | 8.75um–280um |
Inner layer copper thickness | 17.5um–175um | 0.15mm–0.25mm |
Drilling hole diameter (mechanical drill) | 0.25mm–6.00mm | 0.15mm–0.25mm |
Hole diameter (mechanical drill) | 0.20mm–6.00mm | 0.10mm–0.20mm |
Hole Tolerance (Mechanical Drill) | 0.05mm | / |
Hole tolerance (mechanical drill) | 0.075mm | 0.050mm |
Laser Drilling Aperture | 0.10mm | 0.075mm |
Plate thickness aperture ratio | 10:1 | 12:1 |
Solder mask type | Photosensitive green, yellow, black, purple, blue, ink | / |
Minimum Solder Mask Bridge Width | 0.10mm | 0.075mm |
Minimum Solder Mask Isolation Ring | 0.05mm | 0.025mm |
Plug hole diameter | 0.25mm–0.60mm | 0.60mm-0.80mm |
Impedance tolerance | ±10% | ±5% |
Surface treatment type | Hot air leveling, chemical nickel gold, immersion silver, electroplated nickel gold, chemical immersion tin, gold finger card board | Immersion Tin, OSP |
Automatic Solder Paste Printing Machine
AOI Optical Inspection
Smt High-Speed Placement Machine
Nitrogen Reflow Soldering
X-Ray
Three Anti-Paint Spraying Machine
SPI Solder Paste Thickness Tester
Automatic Wave Soldering Machine
First Article Inspection