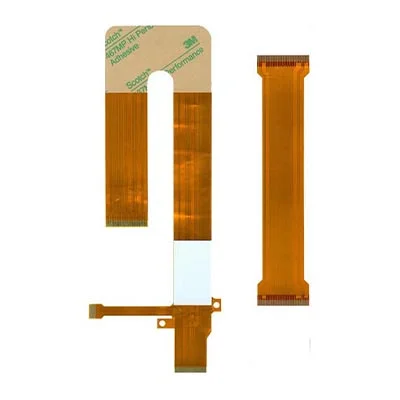
Automotive Dashboard Flexible Circuit Board
Name: Car dashboard soft board
Layers: 2 layers
Plate Thickness: 0.12mm
Material: double-sided non-adhesive electrolytic material
Copper Thickness: 1/2 OZ
Finish: Immersion Gold 1 microinch
Minimum line width/line spacing: 0.08mm/0.075mm
FR4 reinforcement thickness: 0.2mm
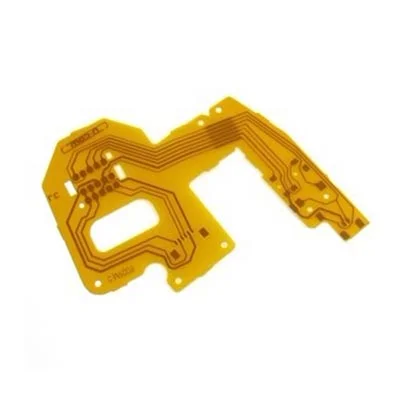
Four-layer impedance fpc circuit board
Name: Four-layer impedance fpc circuit board
Application: Machine Equipment
Type: Four-layer FPC circuit board
Minimum drilling: 0.2mm
Minimum line width/line spacing: 0.1mm/0.1mm
Finished thickness: 0.25+/-0.05mm
Reinforcement: L40.25mmFR4 reinforcement
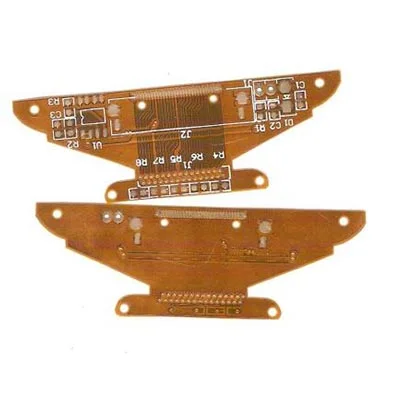
Five-layer vehicle fpc circuit board
Five-layer vehicle fpc circuit board
Application: machine equipment
Type: Four-layer FPC soft board
Minimum drilling: 0.2mm
Minimum line width/line spacing: 0.1mm/0.1mm
Finished thickness: 0.3+/-0.05mm
Reinforcement: 0.4mmFR4 reinforcement on the front and back
Process requirements: differential impedance of 90 ohms +/- 10% ohms
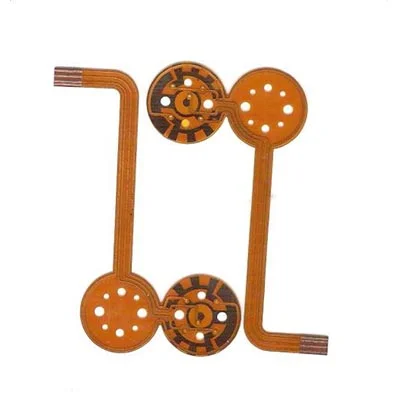
Double-sided smart wearable fpc circuit board
Name: Double-sided smart wearable fpc circuit board
Basic Parameters: Application: Smart Watch
Type: Double-sided FPC circuit board
Line width/line spacing: 0.73mm/0.54mm
Tolerance: +/-0.03mm
Thickness: 0.13mm
Surface treatment: Immersion gold 1u
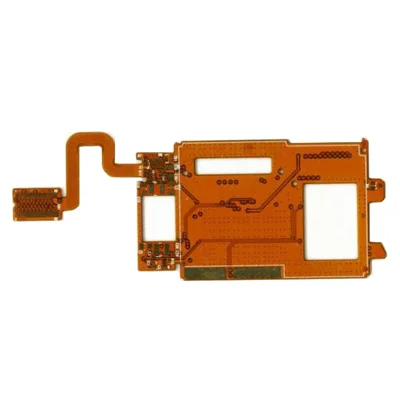
Six-layer Flexible Circuit Board
Name: Six-layer PC impedance board
Application: Machine Equipment
Type: Six-layer FPC circuit board
Minimum drilling: 0.2mm
Minimum line width/line spacing: 0.1mm/0.1mm
Finished thickness: 0.25+/-0.03mm
Reinforcement: 0.25mm steel sheet reinforcement on both sides
Surface treatment: Immersion gold (sand blasting, nickel thickness 120 miles; gold thickness 2 miles)
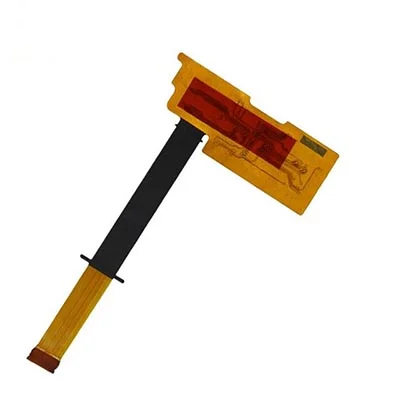
Double-sided FPC flexible circuit board
Name: Double-sided FPC Flexible circuit board
Basic Parameters: Application: Medical Equipment
Type: Double-sided FPC soft board
Size: 70.5*117.2mm
Minimum drilling: 0.15mm
Plate thickness: 0.1mm
Reinforcement: 0.5mm FR4 reinforcement on the back of the pad
Surface treatment: Shen Jin 1 mile
- FPC Fabrication Capability
- PCB manufacturing equipment
Flexible Circuit Boards, or Flex PCBs, are a revolutionary advancement in printed circuit boards. Unlike rigid PCBs, Flex PCBs offer exceptional flexibility, allowing them to bend, twist, and conform to the shape of the device or system they are integrated into.
This flexibility opens up a new realm of possibilities for electronic designs, especially in applications involving space constraints, complex geometries, or dynamic movements.
Flex PCBs find applications in various industries, including consumer electronics, medical devices, automotive systems, wearable technology, aerospace, and more. Their ability to conform to complex shapes and withstand dynamic movements makes them suitable for applications that require flexibility, durability, and reliability.
The fabrication capabilities for flexible printed circuit boards (FPCs) can vary among manufacturers. However, here are some common capabilities associated with FPC fabrication:
- Layer count: FPCs can be manufactured with single-sided, double-sided, or multilayer configurations, depending on the complexity of the circuit design and the requirements of the application. Multilayer FPCs can provide increased functionality and density.
- Substrate materials: FPCs are typically made using flexible materials such as polyimide (PI) or polyester (PET). The choice of substrate material depends on the desired mechanical properties, thermal resistance, and specific application requirements.
- Copper weight and thickness: FPCs can be fabricated with different copper weights and thicknesses to accommodate various current-carrying capacities and design considerations. Common copper thicknesses for FPCs include 0.5 oz, 1 oz, and 2 oz.
- Circuit trace width and spacing: FPC manufacturers can produce circuit traces with precise widths and spacing to meet specific design requirements. The capabilities for trace width and spacing depend on the manufacturing processes and equipment used by the manufacturer.
- Surface finishes: FPCs can be finished with different surface treatments to protect the copper traces and enhance solderability. Common surface finishes include Electroless Nickel Immersion Gold (ENIG), Immersion Silver, HASL (Hot Air Solder Leveling), and OSP (Organic Solderability Preservatives).
- Solder mask and legend printing: FPCs can have solder mask coatings applied to protect the copper traces and prevent solder bridges during assembly. Legend printing is the process of adding component designators and other identifying marks to the board for assembly and troubleshooting purposes.
- Panelization and routing: FPC manufacturers can panelize multiple FPCs on a single panel for efficient production. They can also provide routing services to separate the individual FPCs from the panel while ensuring clean and accurate cuts.
- Quality control and testing: Reputable FPC manufacturers have robust quality control processes in place to ensure that each board meets the specified requirements. They may conduct various tests, such as electrical continuity testing, impedance testing, and dimensional checks, to verify the integrity and performance of the FPCs.
Advantages of Flexible Circuit Boards :
- Space Efficiency: Flex PCBs excel in space-constrained applications where traditional rigid PCBs may not fit or be too bulky. This also makes Flex PCBs ideal for compact electronic devices or systems with irregular shapes.
- Weight Reduction: Flex PCBs are lightweight compared to rigid PCBs, contributing to overall weight reduction in electronic devices. This advantage is especially crucial in aerospace, automotive, and also in portable electronics industries, where weight savings are essential for improved performance and portability.
- High Reliability: Flex PCBs are designed to withstand repetitive bending and flexing without compromising functionality. They are made with specialized materials that offer excellent flexibility, resilience, and durability.
- Enhanced Design Flexibility: Flex PCBs offer unparalleled design flexibility, allowing intricate and three-dimensional circuit layouts. They can be shaped to match the product’s contours, enabling efficient use of available space.
- Increased Signal Integrity: Flex PCBs offer excellent electrical performance and signal integrity. They can be designed with controlled impedance, minimizing signal loss, crosstalk, and electromagnetic interference (EMI). The absence of connectors and cables also reduces the risk of signal degradation.
PCB Drilling machine
PCB pattern plating line
PCB solder mask expose machine
PCB pattern expose machine
Strip film etching line
Solder mask screen silk print machine
Solder mask scrubbing line
PCB Flying Probe Test (FPT)
Fully automatic exposure machine